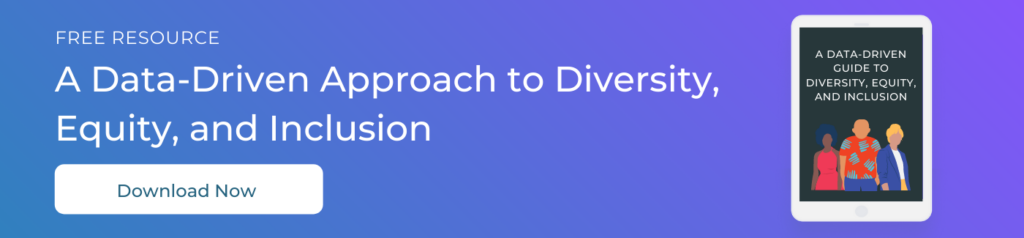
What’s the current context around hiring in manufacturing, and how can technology make the process easier?
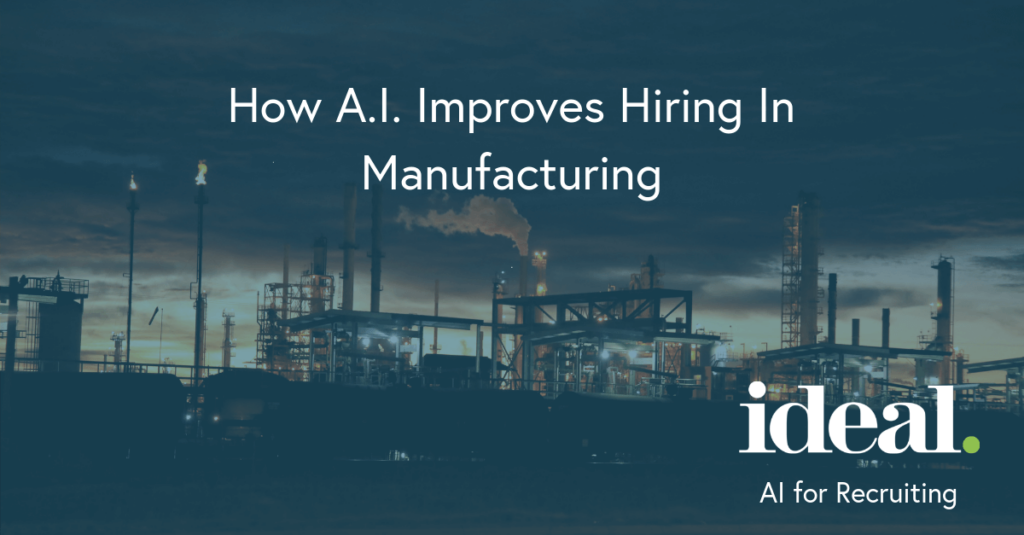
Where we stand now
Recently, as per The Wall Street Journal there is: “Record-high manufacturing job openings, but slow hiring.” This is true: In May 2019, manufacturing job openings hit a record-high, and it’s even a big deal in economies not traditionally tied to manufacturing, such as France. But even though the demand is there, the hiring seems much slower than 2-3 years ago.
There’s also something else to consider: In the early-to-mid-1980s, some major manufacturing companies, such as General Motors, often filled 80-90% of openings from within, i.e. internal movement of employees. Since 2010, that number in similar companies is closer to 33%. A significantly-bigger number of employees are now external fills. That comes about from a lot of factors, including the skills gap of existing employees, but regardless of the exact cause, it means that companies with a strong manufacturing component are filling roles externally (from the market) as opposed to internally (from current employees), and that brings with it increased pressure and the need to be right despite not always having complete information about a candidate. It’s a tricky shift that companies like GM have been making.
How can manufacturers hire more efficiently in 2019 and beyond, then?
Hiring better in manufacturing
Manufacturing hires are often made at high-volume events, i.e. BMW hiring at a massive on-site in Greenville, South Carolina or Phillips 66 using a targeted mobile and on-site campaign for veterans. These approaches do work, but there are other ways to speed up hiring in manufacturing as well — and get better fits for your roles, which improves tenure and reduces turnover. Reduced turnover is obviously a cost savings as well.
Understanding roles: “Manufacturing” is a pretty broad area to discuss, and there are lots of different roles and job descriptions that fall under that bigger umbrella. Some of the bigger categories of manufacturing job roles include assembly workers, brazers and welders, machinists, operators, production managers, quality control inspection, and production workers. There are some job description templates for broader manufacturing categories available online.
Know what you need: In addition to the specific roles you need, understand the broad qualifications of who you need and why. For example, many manufacturing jobs only require a HS degree or GED, but companies look to hire people who can learn quickly, especially for machinist and operator roles. As these roles often work adjacent to machines and the output (the final product) is time-sensitive, you need to make sure candidates are dependable as well.
Screening: Now you’re ready to start the process of building a pipeline of candidates. Screening is among the first things you do. Now, humans are great at analyzing reactions and emotions in a conversation, but they absolutely cannot do resume screening at scale in the way that an artificial intelligence program can. If you’re growing and filling roles quickly, AI-powered HR screening tools are your best path. Think of the sheer math: Even if a human recruiter only spends six seconds per resume (an often cited stat and not something to aspire to), 200 resumes would still take 1,200 seconds, or 20 minutes. 200 resumes can be done by AI in less than 1 minute. Some candidates to these roles might not even have resumes, in which case a chatbot can ask them a few quick questions to better assess if they are qualified for the role.
Candidate communication: This is an essential component of overall candidate experience, and having a positive candidate experience is one major way you get better manufacturing candidates coming into your funnel. Remember: many manufacturing jobs are filled by referral, i.e. this person worked at a previous plant with this other person, and when an operator job opens up, they might recommend their former colleague. But no one wants to be recommended and then walked through a process with lots of screens and forms and little communication about key questions related to the role. You need a way to make your candidate experience better without stressing out or over-working all the human beings in your recruiting department. Here’s one approach: Humans right now have varied feelings on chatbots, up to and including the VP of Talent Management at Diply. But chatbots can be used in clever ways to communicate more effectively with candidates, especially in terms of FAQ-style questions that can be easily addressed by a bot, freeing up humans working hours to spend more time on interviews and gathering role context.
Brief note on integrations: There are so many different software suites that recruiters use now, that integrations are so important. Whatever you do in terms of maximizing your manufacturing hiring, make sure any technology partner integrates with the other systems you use. If systems don’t talk to each other, nothing really gets done. That applies to almost any industry, but people forget about it when shopping for tech. Everything has to work together or the results aren’t productive.
Rediscovery: If you’ve launched similar manufacturing hiring campaigns before, you’ve had candidates who “just missed” the cut. Well, since 2016 we’ve been saying that “the next big thing” in recruiting is candidate rediscovery, where artificial intelligence goes into your “dumb tech” ATS and finds previous candidates who match to current open roles. Reach out to them and see if they’re interested. We talk about “the war for talent” a lot, but in reality, no one wants to go fight a war. You can opt out of the “war” by being smarter about finding people, and that includes finding people already in your system.
The bottom line
There is a potential manufacturing recession on the horizon, especially as seen in input concepts like Japanese tool orders, so hiring effectively in a still-robust time is crucial. Use technology as a force multiplier to get the best people for your business — quickly and securing the right fits, which means a reduction in turnover. The only way you should want to be doing constant manufacturing hiring is if your business is rapidly growing (good!), not because you keep losing people to turnover (bad!). Find the right people and find them quickly. That’s where tech + humans work the best.